网站公告:
产品展示
最新信息
联系我们
名称:上海顾高能源科技有限公司
联 系人:顾先生
手 机:13701742848
Q Q :1085003134
网 址:www.688si.com
邮 箱:1085003134@qq.com
地 址:上海浦东成山路3188号
电池片回收新闻
电池工艺对组件衰减的影响
2017-6-10 来源: 作者:佚名 阅读:次 【打印此页】
电池工艺对组件衰减的影响
多晶硅电池片经封装成组件,功率会有相应的损失,称之为封装损耗。多晶硅电池工艺中细微的差异就会导致组件衰减的不同。针对氮化硅膜厚与折射率、扩散均匀性、电池片摩擦情况引起的组件衰减进行了详细的研究,通过优化相关的参数,有效提升工艺质量,降低功率损失。
电池片的生产过程是极其重要的一个过程,工艺参数的稳定性及差异性会对电池片的功率输出造成极大的波动,间接引起组件衰减过大,产品不合格。基于此,本文从电池片生产过程的一些重要环节入手,找出其中存在的问题,加以优化改进,提高产品质量,节约成本。
1电池工艺对组件功率损失的分析
1.1光学损耗
地面用硅太阳能电池的光谱响应范围一般为300nm~1100nm,因此,任何这一波段的光进入电池都会造成光学上的损失[1]。可以从光的透射和反射两方面进行分析[2]。太阳能多晶电池的表面会沉积一层减反射膜,即氮化硅膜,做成组件之后其上有EVA和钢化玻璃(两者的折射率约为1.48左右),如图1所示。为使组件的透射率达到最大的减反效果,还需要使SiNx膜的折射率、EVA和玻璃的折射率得到最好的匹配结果和最佳光学上的减反射效果,这样可以有效地增加组件的输出功率。
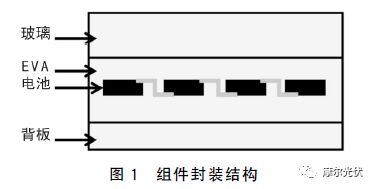
增透膜是根据薄膜干涉原理,在介质表面镀一层或多层薄膜,可以有效减少光的反射,这种膜就是减反射膜[3]。当光垂直入射时,介质表面的反射率见式(1):
式中:ns为硅折射率;n0为大气折射率。
当在介质表面镀一层减反射膜时,光在薄膜表面的反射会在上表面产生薄膜干涉,从而减少光的反射。此时,反射率表达式为式(2):
其中,r1,r2分别是光在空气-薄膜、薄膜-介质界面上的反射系数,
,Δ为相位角, ;λ0为入射光波长;n为薄膜折射率;d为薄膜厚度;nd为薄膜光学厚度。在光垂直入射时,若薄膜光学厚度为1/4波长,即nd=λ0/4,则见式(3):
当Rλ0为零时,则:
依据上述原理可根据组件钢化玻璃或镀膜玻璃与EVA的不同折射率,设计相应的氮化硅薄膜的折射率,达到组件的光学最佳匹配。
1.2电学损失
电池引起的电学损耗包括电池片串联时电流不匹配、焊条与电极的接触电阻、扩散方阻不均匀引起的功率损失、电池片边缘摩擦后引起边缘短路等。本文主要研究扩散方阻不均匀与电池摩擦的电学损失。扩散方阻不均匀是指扩散之后,硅片出现部分扩散不到区域,此区域方阻值较大,容易造成漏电过大和电池片串阻过高。接受光照时,因方阻不均匀,电池片方阻较小区域容易发热过高,导致电池片温度升高,继而引起效率降低。图2、图3为扩散不均匀硅片与EL图像。
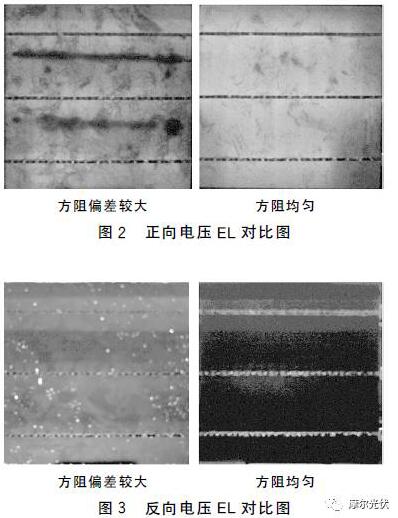
摩擦功损主要存在于使用湿法刻边工艺的电池片中,电池片经丝网印刷烧结之后,皮带传输、质检分选、组件焊接等过程中片与皮带、片与片之间摩擦时造成边缘残留金属粉粒,从而导致漏电增大,效率降低。
2实验方案与分析
2.1PECVD的配方优化实验[4]
设计2组不同折射率的双层氮化硅膜实验,一组以空气、双层氮化硅、硅片为光传输介质;另一组以钢化玻璃与EVA、双层氮化硅、硅片为传输介质。根据 ,已知空气折射率为1.0、组件钢化玻璃与EVA的折射率为1.48,硅的折射率为2.76,可计算出2组氮化硅双层膜的折射率。选取电池吸收波长能量最大的600nm计算相应的双层膜厚。将上述2组材料做成组件测试其衰减情况,封装结果见表1。
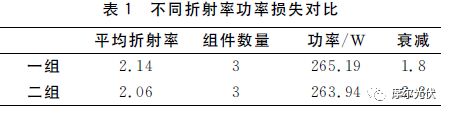
2.2扩散方阻不均匀的实验
选取2组扩散实验片,每组600片,一组片内偏差较大,二组方阻均匀,共制作6块组件。图4为2组组件的EL图,由图4可看出,偏差较大分组EL图像中明显存在偏暗或偏亮的区域。
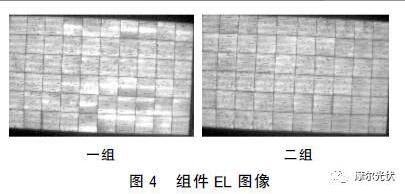
表2为组件测试数据,由表2数据看出,片内方阻偏差较大的功率损失较大,主要因为,方阻偏差较大,电池片内部电流分布不均匀,导致局部结浅,串联电阻较大,同时容易导致漏电增大,最终导致功率损失变大。
2.3电池片摩擦实验
选取2组相同效率段电池片,每组10片,一组使用激光切边,二组为正常湿法切边,人为模拟片与片之间的摩擦,观察摩擦前后的数据。表3、表4分别为摩擦前、后的数据对比。由表4数据看出,激光切边摩擦前、后的数据比较稳定,而湿法切边摩擦前、后的数据对比差距比较明显,主要表现在并阻降低、反向电流升高、填充降低。
电池片的生产过程是极其重要的一个过程,工艺参数的稳定性及差异性会对电池片的功率输出造成极大的波动,间接引起组件衰减过大,产品不合格。基于此,本文从电池片生产过程的一些重要环节入手,找出其中存在的问题,加以优化改进,提高产品质量,节约成本。
1电池工艺对组件功率损失的分析
1.1光学损耗
地面用硅太阳能电池的光谱响应范围一般为300nm~1100nm,因此,任何这一波段的光进入电池都会造成光学上的损失[1]。可以从光的透射和反射两方面进行分析[2]。太阳能多晶电池的表面会沉积一层减反射膜,即氮化硅膜,做成组件之后其上有EVA和钢化玻璃(两者的折射率约为1.48左右),如图1所示。为使组件的透射率达到最大的减反效果,还需要使SiNx膜的折射率、EVA和玻璃的折射率得到最好的匹配结果和最佳光学上的减反射效果,这样可以有效地增加组件的输出功率。
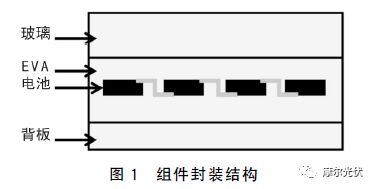
增透膜是根据薄膜干涉原理,在介质表面镀一层或多层薄膜,可以有效减少光的反射,这种膜就是减反射膜[3]。当光垂直入射时,介质表面的反射率见式(1):
式中:ns为硅折射率;n0为大气折射率。
当在介质表面镀一层减反射膜时,光在薄膜表面的反射会在上表面产生薄膜干涉,从而减少光的反射。此时,反射率表达式为式(2):
其中,r1,r2分别是光在空气-薄膜、薄膜-介质界面上的反射系数,
,Δ为相位角, ;λ0为入射光波长;n为薄膜折射率;d为薄膜厚度;nd为薄膜光学厚度。在光垂直入射时,若薄膜光学厚度为1/4波长,即nd=λ0/4,则见式(3):
当Rλ0为零时,则:
依据上述原理可根据组件钢化玻璃或镀膜玻璃与EVA的不同折射率,设计相应的氮化硅薄膜的折射率,达到组件的光学最佳匹配。
1.2电学损失
电池引起的电学损耗包括电池片串联时电流不匹配、焊条与电极的接触电阻、扩散方阻不均匀引起的功率损失、电池片边缘摩擦后引起边缘短路等。本文主要研究扩散方阻不均匀与电池摩擦的电学损失。扩散方阻不均匀是指扩散之后,硅片出现部分扩散不到区域,此区域方阻值较大,容易造成漏电过大和电池片串阻过高。接受光照时,因方阻不均匀,电池片方阻较小区域容易发热过高,导致电池片温度升高,继而引起效率降低。图2、图3为扩散不均匀硅片与EL图像。
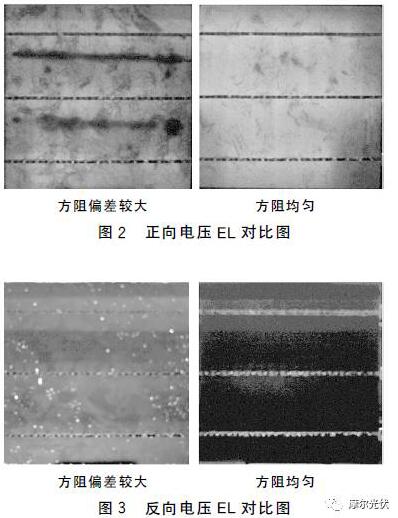
摩擦功损主要存在于使用湿法刻边工艺的电池片中,电池片经丝网印刷烧结之后,皮带传输、质检分选、组件焊接等过程中片与皮带、片与片之间摩擦时造成边缘残留金属粉粒,从而导致漏电增大,效率降低。
2实验方案与分析
2.1PECVD的配方优化实验[4]
设计2组不同折射率的双层氮化硅膜实验,一组以空气、双层氮化硅、硅片为光传输介质;另一组以钢化玻璃与EVA、双层氮化硅、硅片为传输介质。根据 ,已知空气折射率为1.0、组件钢化玻璃与EVA的折射率为1.48,硅的折射率为2.76,可计算出2组氮化硅双层膜的折射率。选取电池吸收波长能量最大的600nm计算相应的双层膜厚。将上述2组材料做成组件测试其衰减情况,封装结果见表1。
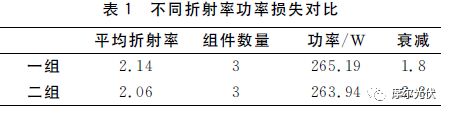
2.2扩散方阻不均匀的实验
选取2组扩散实验片,每组600片,一组片内偏差较大,二组方阻均匀,共制作6块组件。图4为2组组件的EL图,由图4可看出,偏差较大分组EL图像中明显存在偏暗或偏亮的区域。
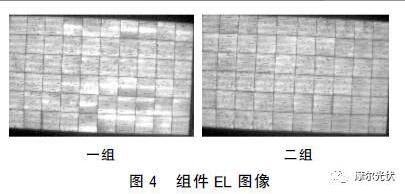
表2为组件测试数据,由表2数据看出,片内方阻偏差较大的功率损失较大,主要因为,方阻偏差较大,电池片内部电流分布不均匀,导致局部结浅,串联电阻较大,同时容易导致漏电增大,最终导致功率损失变大。

2.3电池片摩擦实验
选取2组相同效率段电池片,每组10片,一组使用激光切边,二组为正常湿法切边,人为模拟片与片之间的摩擦,观察摩擦前后的数据。表3、表4分别为摩擦前、后的数据对比。由表4数据看出,激光切边摩擦前、后的数据比较稳定,而湿法切边摩擦前、后的数据对比差距比较明显,主要表现在并阻降低、反向电流升高、填充降低。
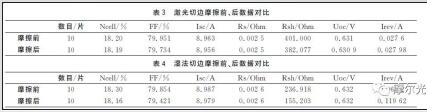
使用显微镜观察摩擦前、后电池片边缘,如图5所示。
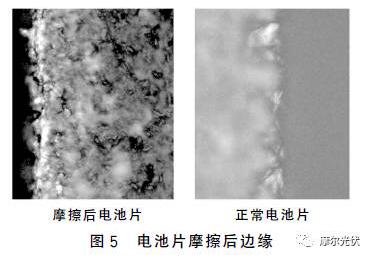
由图5看出,摩擦后电池片边缘会出现亮点,分析其成分应为浆料,正是其导致摩擦后边缘短路;而激光切边后因为激光切断正面边缘PN结,即使边缘残留浆料粉末,也不影响其导电性。
3结论
组件的功率损失分为光学损失与电学损失,光学损失可通过优化氮化硅的折射率,匹配组件玻璃与EVA;电学损失中,扩散不均匀需调整扩散配方参数、制绒表面均匀性降低片内偏差[5];电池摩擦可采用每日清洗传输皮带、变更质检检片手法等方式解决。
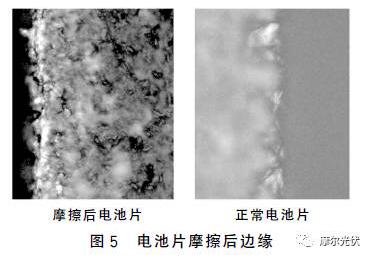
由图5看出,摩擦后电池片边缘会出现亮点,分析其成分应为浆料,正是其导致摩擦后边缘短路;而激光切边后因为激光切断正面边缘PN结,即使边缘残留浆料粉末,也不影响其导电性。
3结论
组件的功率损失分为光学损失与电学损失,光学损失可通过优化氮化硅的折射率,匹配组件玻璃与EVA;电学损失中,扩散不均匀需调整扩散配方参数、制绒表面均匀性降低片内偏差[5];电池摩擦可采用每日清洗传输皮带、变更质检检片手法等方式解决。
上一篇:
P型单晶电池衰减原因与改善